Organ Blower Upgrade
The “New†Spencer Steel Orgoblo #11887
Installed May, 2016
written by Tim Wilson, donor
Installed May, 2016
written by Tim Wilson, donor
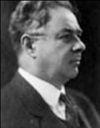
Ira Spencer
The Spencer Turbine Company of Hartford, Connecticut, became known for manufacturing one of the finest and most dependable pipe organ blowers in the industry... as an interesting application of its industrial turbines. The company, founded by Ira Hobart Spencer, began manufacturing turbines in 1892. Mr. Spencer is known as one of America’s legendary inventors and entrepreneurs. Led by his passion for the pipe organ at his own church, he charged his corporate dynasty to apply his air-moving technology to the pipe organ in order to supply the instrument with an efficiently produced wind supply. To this point in pipe organ building, wind was provided by human physical labor, pumping air through a complex set of bellows - a very tedious chore. The result is what has become known as the “Spencer Steel Orgoblo.†In 1904, the company began manufacturing organ blowers in their new “Organ Power Division.†Spencer remains in operation today in Windsor, Connecticut, but they ceased manufacturing their Orgoblo in 1986. During an eighty-one year span of time, they manufactured and sold over 31,000 blowers, many of which are still in existence today, giving rise to the notion that the Spencer Orgoblo is the Lincoln of organ blowers.
Figuring there must be a better way to move air into the pipes of an organ other than by way of demanding physical labor, Spencer first invented a water-powered hydraulic engine to do the job. Soon, he had a flourishing business installing water motors for church organs all over the country. When electricity finally became common in buildings, he capitalized on this resource by switching his water-powered blower to electrically powered ones with a completely redesigned machine. His new blower was called the Orgoblo, a name simply derived from exactly what it is, an organ blower. This design incorporated the trademarked “sugar scoop†housing profile that has become its single-most recognizable characteristic. To this day, Spencer continues to furnish spare parts for some of the early blowers still in service, such as #11887, newly installed here at First United Methodist Church.
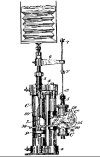
The Spencer Water Motor
Not the first Orgoblo at First United Methodist Church

Our original Spencer Orgoblo
#11887 is not the first Spencer blower to provide wind for the Johnson & Son pipe organ at First United Methodist Church in London; it is the fourth. The first blower, the organ’s original blower, was one of Spencer’s water-powered blowers. The second blower was one of the new-fangled electric blowers. First Methodist was on board quite early, only two years after major production of the new electric blower began in 1906, to purchase one, but not for ten years after London began using electricity. This second blower provided wind for 77 years, from the time the organ was still a mechanical action instrument through the 1959 conversion to electro-pneumatic action, and up to 1985.
Then in 1985, Kichline Organ Service recommended that the 1906 Orgoblo be replaced with a larger blower, as it proved to be inadequate after the installation of a high pressure reservoir on the large 16’ open diapason in the pedal division. The 1906 blower was disassembled, removed, and stored in the church garage. Some years later, Richard Kichline purchased it for an instrument more suited to its capacity in northeast Ohio. A new Orgoblo, #31343, was installed. I was quite a young man then, but not too young to realize that this new blower wasn’t manufactured like older models. It sounded like a grain dryer. It was loud. It noisily roared away in the blower room in the lower level. Surely something was wrong with it. We had it rebalanced. It was double- and triple-checked but still, it was noisy. We were forced to live with it. In spite of its noisiness, #31343 served our organ until May 2016. During those years, it performed its job quite adequately.
But during the 2010 organ renewal project, several changes and additions were made. The 1985 blower, only 25 years old at the time, seemed to handle the greater demands placed upon it by the changes and additions. We were happy with the instrument and never noticed any inadequacy of wind.
But during the 2010 organ renewal project, several changes and additions were made. The 1985 blower, only 25 years old at the time, seemed to handle the greater demands placed upon it by the changes and additions. We were happy with the instrument and never noticed any inadequacy of wind.
“Short on Windâ€
Our Johnson & Son pipe organ has been played by many fine concert artists from Columbus, Springfield, Michigan, Indianapolis, and Washington DC. They’ve always marveled at the beauty of the organ itself, but they thought it was “short on wind.†What does this mean? Without going into an overly detailed analysis of wind pressure and the role it plays in the function of a pipe organ, suffice it to say that the 1985 blower couldn’t produce enough wind to make our instrument function properly when an organist would use it to its fullest capacity... when it is being played at its loudest. Certainly, organists make such a demand on the organ only occasionally. So, the lack of wind was noticeable only infrequently during regular service playing ~ but during a concert, more often. To the ear, one could hear a sag in pitch at these moments! The instrument was functioning quite handsomely, but not at its best.
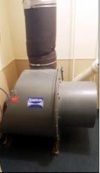
The 1985 Spencer Orgoblo
As a pipe organ aficionado and chairperson of the board of trustees at First Church, I’ve championed many projects related to the physical property of the church, as charged by the Discipline of the United Methodist church. This includes the pipe organ. So, I called our organ technician, John Muller of Muller Pipe Organ, to study our 1985 Orgoblo. Is it inadequate for the instrument itself or are all these fine organists wrong in saying it is “short on wind?†John calculated the actual amount of wind needed by our organ and indeed discovered that the blower was shy an adequate wind supply by almost 200 cubic feet per minute (CFM). Not only was it too small to produce the required 1,400 CFM, but it barely could generate enough wind to keep the static pressure at four inches, the amount required to make the organ function properly when it is played to full capacity. We concluded that the organ needed more wind... which meant needing a new, more powerful blower.
Over many years, we’ve worked tirelessly to keep our wonderful instrument true to its original design as much as possible. Additions have been specially executed to maintain the overall style of the instrument as it was originally designed. With that, I thought it would be in keeping with this general philosophy to find another Orgoblo that would adequately supply it with wind. But they haven’t been manufactured since 1985. We already had one of the last ones produced. Ours was #31343, third from the last one, #31345. What to do? I knew the older Spencer blowers were built like tankers, so there simply had to be one out there in the world that had survived decades of usage that would be ideal for our organ. I knew that the older blowers operated more quietly than the latest models made by Spencer. It seemed a dream to have such a blower for our organ. I finally arrived at the idea of trying to locate an Orgoblo that was similar in age to our organ. John Muller knew of one being available.
Over many years, we’ve worked tirelessly to keep our wonderful instrument true to its original design as much as possible. Additions have been specially executed to maintain the overall style of the instrument as it was originally designed. With that, I thought it would be in keeping with this general philosophy to find another Orgoblo that would adequately supply it with wind. But they haven’t been manufactured since 1985. We already had one of the last ones produced. Ours was #31343, third from the last one, #31345. What to do? I knew the older Spencer blowers were built like tankers, so there simply had to be one out there in the world that had survived decades of usage that would be ideal for our organ. I knew that the older blowers operated more quietly than the latest models made by Spencer. It seemed a dream to have such a blower for our organ. I finally arrived at the idea of trying to locate an Orgoblo that was similar in age to our organ. John Muller knew of one being available.
Our “New†Spencer Steel Orgoblo #11887
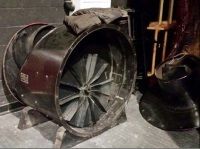
#11887 on the stage in Ashtabula
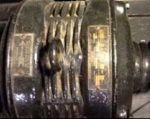
Westinghouse motor before restoration
Being in the organ building and restoration business, John Muller learned of an Orgoblo that was available at the Lakeside High School Performing Arts Center in Ashtabula, Ohio. I called William Hill of the Lakeside Music Booster Organ Committee to find out about the blower. He explained that the blower originally belonged to a 1921 W.W. Kimball theatre-style pipe organ that they had acquired for installation in their facility. But for their installation, additions were to be made to the instrument... making its Orgoblo too small. Mr. Hill had been charged with procuring a bigger blower (which they did - a very large 10hp Spencer) and finding a new home for the original one - #11887.
I was thrilled to learn that their blower, #11887, built 95 years ago, though inadequate for their instrument, would be more than adequate for our organ here in London. It was designed to deliver 8 inches of static pressure and 2,250 cubic feet of wind per minute, both much more than our instrument would ever need! Its age was ideal for our 122-year-old organ. I was ready to go after it until I learned that the blower’s Westinghouse induction motor operated on three-phase electricity. We don’t have three-phase electricity at First Church.
I was thrilled to learn that their blower, #11887, built 95 years ago, though inadequate for their instrument, would be more than adequate for our organ here in London. It was designed to deliver 8 inches of static pressure and 2,250 cubic feet of wind per minute, both much more than our instrument would ever need! Its age was ideal for our 122-year-old organ. I was ready to go after it until I learned that the blower’s Westinghouse induction motor operated on three-phase electricity. We don’t have three-phase electricity at First Church.
Not one to give up easily, I was determined the problem could be solved. I called Mike Mosier of Ohio Electric Motor Service Center. If there were anyone who knew about such things, it would be Mike. Indeed, he did! A variable frequency drive (VFD) could be installed. This device would operate the motor and give flexibility over speed and other aspects of a motor’s function ~ modern technology is a great thing! Mike must have sensed my excitement about the new (old!) blower and offered to help in any way he could. With that, I knew the Ashtabula blower soon would have a new home here in London! Mike Mosier lives in South Charleston and we’ve been friends for years. When it comes to electric motors, his company is the “real deal†in Columbus!
Knowing that the Ashtabula blower would work for our organ, I called Bill Hill to look into purchasing it. I was shocked to learn that the Lakeside Music Booster Organ Committee was happy to donate the Orgoblo to a new home. They didn’t want to sell it... they wanted it to go free of charge to a new home. Without hesitation I said, “Consider it donated to First United Methodist Church in London, Ohio!â€
The very next day I sent Paul Richards, an employee of Wilson Printing & Graphics, and Lindsey Gibbs, to fetch the blower. Off to Ashtabula they went. The blower had already been disassembled down to its major components, which made transporting it home very easy. But it wasn’t until we unloaded it at Wilson Printing that we realized that it was... HUGE! I worried... was it too large for its designated space at church? I had measured time and time again before deciding to pursue the project, so I was confident, but actually seeing it made me panic! Happily, my panic was abated after a visit to the blower room, measuring tape in hand! The only concern, slight as it was, was that a plumbing pipe may need to be adjusted.
Knowing that the Ashtabula blower would work for our organ, I called Bill Hill to look into purchasing it. I was shocked to learn that the Lakeside Music Booster Organ Committee was happy to donate the Orgoblo to a new home. They didn’t want to sell it... they wanted it to go free of charge to a new home. Without hesitation I said, “Consider it donated to First United Methodist Church in London, Ohio!â€
The very next day I sent Paul Richards, an employee of Wilson Printing & Graphics, and Lindsey Gibbs, to fetch the blower. Off to Ashtabula they went. The blower had already been disassembled down to its major components, which made transporting it home very easy. But it wasn’t until we unloaded it at Wilson Printing that we realized that it was... HUGE! I worried... was it too large for its designated space at church? I had measured time and time again before deciding to pursue the project, so I was confident, but actually seeing it made me panic! Happily, my panic was abated after a visit to the blower room, measuring tape in hand! The only concern, slight as it was, was that a plumbing pipe may need to be adjusted.
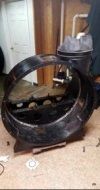
"Sugar Scoop" housing
almost completely
disassembled
almost completely
disassembled
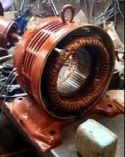
Re-wound 1921
Westinghouse Motor
Westinghouse Motor
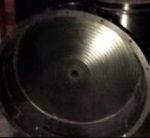
Inside of
"sugar scoop" housing -
before restoration
"sugar scoop" housing -
before restoration
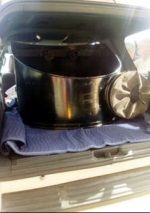
11887 loaded in back
of my Ford Expedition
of my Ford Expedition
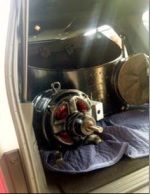
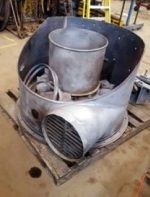
#11887 after being
baked and
sand blasted
baked and
sand blasted
The blower seemed to be in good condition. It was dirty and we could see that some minor repairs had been made. Other than finding some caulk that had been used to seal gaps in the worn felt, everything looked great. Paul, Kevin Lohr, and I began taking the rest of the “sugar scoop†housing apart. We handled countless parts: the motor plate, the motor mounts, the wooden saddle bases, a myriad of screws and bolts. The following day, we took the pile of blower parts to Ohio Electric Motor Service Center. Mike had his staff bake it to remove all the old paint and then they sandblasted it. It was spotless! When Mike and his crew rewound the motor, they found the bearings and the shaft to which the turbines are attached to be in perfect condition.
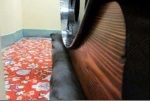
refinished wooden cradle base
We then took the thoroughly cleaned steel parts to my awesome friends at Buckeye Ford in London. Jim, Jan, and Jason Hunt agreed to paint the blower as a donation to the church. Kathy Beckwith, the body shop manager, coordinated the schedule. They primed and painted all the parts with a three-stage epoxy gloss black. The finished pieces looked amazing... just like the body of a new car! The Buckeye Ford crew really worked magic as a quick visual inspection of #11887 certainly shows. As John Muller said, “they never looked that good when they came from Spencer.â€
While all of these larger aspects of #11887’s restoration were in process, we worked on other equally important details of the project. Traver Litchfield at Dwyer’s Hardware Store rounded up new stainless steel bolts, washers, and nuts. Kevin stripped and sanded the wooden cradle bases and finished them with stain. We believe them to be solid mahogany! I think this blower probably is the only Spencer Orgoblo in the world that has naturally finished wooden cradle bases!
While all of these larger aspects of #11887’s restoration were in process, we worked on other equally important details of the project. Traver Litchfield at Dwyer’s Hardware Store rounded up new stainless steel bolts, washers, and nuts. Kevin stripped and sanded the wooden cradle bases and finished them with stain. We believe them to be solid mahogany! I think this blower probably is the only Spencer Orgoblo in the world that has naturally finished wooden cradle bases!
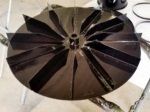
Newly painted turbine blade
at Buckeye Ford
at Buckeye Ford
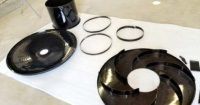
Motor plate, intake tube,
bands and finned
separator plate
bands and finned
separator plate
A very special aspect of the blower project was the restoration of the small name and data plates. We’ve all seen similar plates on various pieces of machinery. They are painted, stamped aluminum, and they carry important information about a machine that warrants more than paper: horsepower, RPM, serial number, blower rotation, and many other details. The plates on our blower were still intact, but they were dirty and worn. Neil Pierce, the offset press operator at Wilson Printing, took on the tedious task of revitalizing them. He stripped them, repainted them, and then carefully sanded the fresh paint off the embossed lettering so it would show. Finally, he sealed them with a clear gloss coating. Neil’s careful work really paid off, as the plates now are the crowning jewels of the blower.
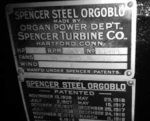
Data Plate - Before
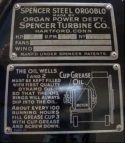
Data Plate - After
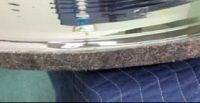
Genuine Spencer Felt on the
edge of the motor plate
edge of the motor plate
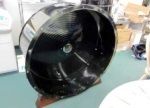
Partially assembled blower
ready for the turbines
ready for the turbines
An Orgoblo is designed and manufactured in sections. Because the assembled blower must be airtight, the sections are sealed together with industrial-grade felt. Since I already knew that the Spencer Company supplied parts for their blowers, I thought I’d call them in hope of receiving some guidance about replacing the felt. Sure enough, they supply the felt! The box of new felt arrived only five days after ordering it; every piece was exactly cut for our blower.
After we assembled the main components of the blower at Wilson Printing, we took it back to Ohio Electric Motor Service Center to have the newly re-wound Westinghouse motor re-installed. Mark Pfeiffer and I worked on reinstalling it, the two turbines, and the front housing. It was ready for a test run! When we first powered it up with just one of the turbines, its power seemed amazing. When we added the second turbine, I knew right then that we wouldn’t have any winding troubles at First Church.
Our Orgoblo was nearly ready for installation. But we simply couldn’t interrupt the usability of the organ for choir practice and service playing. I knew it would be possible to get the blower installed without a break in the organ’s function, but it would take careful coordination and cooperation from many people to get the job done from a Sunday after church service to the following Thursday evening’s choir practice. With this aspect of the project, many things had to happen in a deliberate order; one thing had to be done before the next thing could even begin.
After we assembled the main components of the blower at Wilson Printing, we took it back to Ohio Electric Motor Service Center to have the newly re-wound Westinghouse motor re-installed. Mark Pfeiffer and I worked on reinstalling it, the two turbines, and the front housing. It was ready for a test run! When we first powered it up with just one of the turbines, its power seemed amazing. When we added the second turbine, I knew right then that we wouldn’t have any winding troubles at First Church.
Our Orgoblo was nearly ready for installation. But we simply couldn’t interrupt the usability of the organ for choir practice and service playing. I knew it would be possible to get the blower installed without a break in the organ’s function, but it would take careful coordination and cooperation from many people to get the job done from a Sunday after church service to the following Thursday evening’s choir practice. With this aspect of the project, many things had to happen in a deliberate order; one thing had to be done before the next thing could even begin.
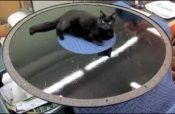
Bart the cat approves
of the felt on the inside
of the intake plate
of the felt on the inside
of the intake plate
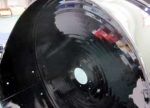
Motor side of first plate
GETTING IT INSTALLED
SUNDAY, MAY 8, 2016
The first step was to remove the 1985 blower. Right after worship service, Bryan and Owen Shoemaker and I dismantled it and removed it from the blower room. We wanted the room to be neat and clean for the new blower, so we readied it for a makeover. We removed the carpeting, washed the walls, and filled holes with spackle. The room was ready to be painted.
MONDAY, MAY 9, 2016
The Blower Room
Sarah Graham - Pastor Steve’s wife got an early start at painting. A fresh coat of paint did wonders for the blower room!
The first step was to remove the 1985 blower. Right after worship service, Bryan and Owen Shoemaker and I dismantled it and removed it from the blower room. We wanted the room to be neat and clean for the new blower, so we readied it for a makeover. We removed the carpeting, washed the walls, and filled holes with spackle. The room was ready to be painted.
MONDAY, MAY 9, 2016
The Blower Room
Sarah Graham - Pastor Steve’s wife got an early start at painting. A fresh coat of paint did wonders for the blower room!
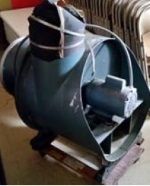
1985 blower removed to storage
and will be offered for sale
and will be offered for sale
Electrical Work
Next was electrical work. The electric service was safe, but shabby. With the room under transformation, the time was ideal for neatening up and updating the wiring from 1959. All wiring between the organ upstairs and the blower room was replaced. My cousin-in-law, Doug Peterman of MCE Electric, and his assistant Dustin Redding, did this work. They also moved the 12-volt direct current power supply from the blower room to the organ chamber. This power supply runs the electro-pneumatic chests and switching mechanism. Believe it or not, this relocation decreased the amount of time the slow-moving 12-volt current took to get from the blower room downstairs to upstairs where the power is actually needed, which we think ultimately made the mechanisms of the organ function more efficiently. Finally, Doug and Dustin installed a new breaker-switch style disconnect box as well as a new contactor that turns on the DC power and chime action in the organ chamber. It also turns on Orgoblo when the organ is switched on at the console.
The Blower Arrives
A large crane truck from Ohio Electric Motor Service Center arrived in the afternoon with the blower strapped in the bed. The crane lifted it off the truck onto a dolly. We moved it downstairs in the elevator. Later that day, Bob McCombs of McCombs Flooring laid remnant pieces of our sanctuary carpeting in the blower room. At this point, we thought the blower room was ready.
Next was electrical work. The electric service was safe, but shabby. With the room under transformation, the time was ideal for neatening up and updating the wiring from 1959. All wiring between the organ upstairs and the blower room was replaced. My cousin-in-law, Doug Peterman of MCE Electric, and his assistant Dustin Redding, did this work. They also moved the 12-volt direct current power supply from the blower room to the organ chamber. This power supply runs the electro-pneumatic chests and switching mechanism. Believe it or not, this relocation decreased the amount of time the slow-moving 12-volt current took to get from the blower room downstairs to upstairs where the power is actually needed, which we think ultimately made the mechanisms of the organ function more efficiently. Finally, Doug and Dustin installed a new breaker-switch style disconnect box as well as a new contactor that turns on the DC power and chime action in the organ chamber. It also turns on Orgoblo when the organ is switched on at the console.
The Blower Arrives
A large crane truck from Ohio Electric Motor Service Center arrived in the afternoon with the blower strapped in the bed. The crane lifted it off the truck onto a dolly. We moved it downstairs in the elevator. Later that day, Bob McCombs of McCombs Flooring laid remnant pieces of our sanctuary carpeting in the blower room. At this point, we thought the blower room was ready.
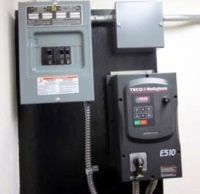
New modern electrical circuits,
replacing fuses from the 1950's.
The VFD is shown at right.
replacing fuses from the 1950's.
The VFD is shown at right.
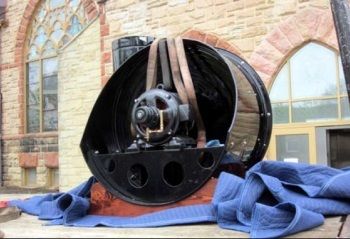
On the crane truck
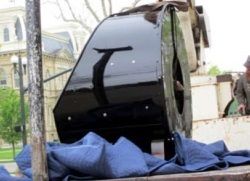
Just before being hoisted onto dolly
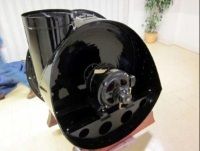
Just off of the elevator
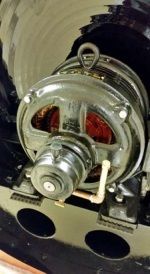
1921 Westinghouse
3 horsepower motor
3 horsepower motor
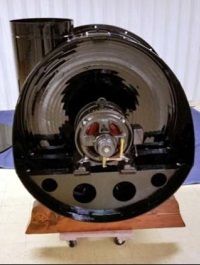
Shiny like a new car!
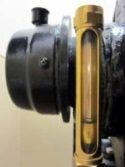
Antique oil indicators showing the oil level for the sleeve bearings. A classy touch from Mike Mosier |
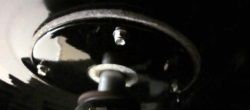
Genuine Spencer felt bearing and motor plate |
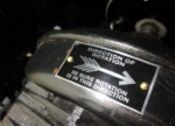
Restored motor direction plate
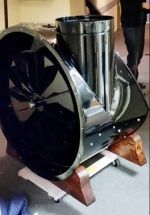
One of the large
31 inch turbine blades
31 inch turbine blades
TUESDAY, MAY 10, 2016
The next task was to position #11887 into the blower room. As we readied ourselves for this task, we realized a plumbing pipe was too close for comfort. We could have left it as it was, but there would have been little to no room behind the blower. I called Tim Barker and Brian Hampton, our plumbers here at First Church. They were able to come right away. Any delay at this point would have jeopardized meeting our goal of having the blower up and running by Thursday night’s choir rehearsal. The plumbing matter was resolved. By moving a drain pipe, we gained 6½ additional inches to work with, which was like gaining 6½ feet; there was very little room to spare!
WEDNESDAY, MAY 11, 2016
We were on mark with every aspect of the installation so far. Stan Osborn from Muller Pipe Organ arrived in the morning to make the final connections on the relocated direct current power supply in the organ chamber. Mike was on hand to program the VFD. And Gene made final adjustments to the connection line.
The next task was to position #11887 into the blower room. As we readied ourselves for this task, we realized a plumbing pipe was too close for comfort. We could have left it as it was, but there would have been little to no room behind the blower. I called Tim Barker and Brian Hampton, our plumbers here at First Church. They were able to come right away. Any delay at this point would have jeopardized meeting our goal of having the blower up and running by Thursday night’s choir rehearsal. The plumbing matter was resolved. By moving a drain pipe, we gained 6½ additional inches to work with, which was like gaining 6½ feet; there was very little room to spare!
WEDNESDAY, MAY 11, 2016
We were on mark with every aspect of the installation so far. Stan Osborn from Muller Pipe Organ arrived in the morning to make the final connections on the relocated direct current power supply in the organ chamber. Mike was on hand to program the VFD. And Gene made final adjustments to the connection line.
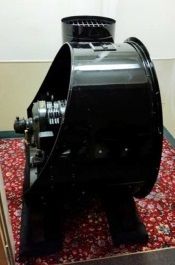
#11887 set in place in blower room
READY, SET, GO
The moment of truth had arrived! Even after several dry-run tests of the blower and its many connections, I still had the jitters! I had no real reason to feel this was because the entire project had been executed by skilled, professional technicians. Not yet knowing the ideal revolutions per minute (RPMs) needed to deliver the required four inches of wind, Mike set the motor to begin at 500 RPMs, 700 RPMs less than its top speed. #11887 was designed to deliver eight inches of static pressure, so we knew we wouldn’t need to run the motor at full capacity. Stan was ready to test the static pressure with a wind gauge meter.
I flipped on the main power switch at the console. The blower started. Stan’s meter indicated the static pressure to be too low, 2.7 inches of wind. We needed more RPMs, so Mike increased the speed to 900, still below its capacity of 1,200. The meter indicated 4.3 inches... BINGO! The moment had arrived to hear the organ at full throttle with an adequate wind supply! I pulled on every stop and played a HUGE chord. I was practically standing on the pedals! The sound was glorious... no sag in pitch whatsoever. Stan’s meter indicated that the static pressure, which naturally drops when the organ is demanding its maximum amount of wind, dropped only slightly to 4.1. This is a most ideal situation for any pipe organ. We truly had solved the problem. No more “short on wind†comments! Not only did we solve the wind problem, we solved a noise issue in the lower level of the church as well. This “new†old blower is twice the size of the 1985 model and is 95 years old, yet it runs trememdously smoother and quieter.
This project has been a labor of love. I am thrilled, pleased beyond words, and forever indebted to many businesses and individuals, listed below, for their input toward bringing a new energy in sound to our Johnson & Son pipe organ here at First United Methodist Church for the praise and worship of God and Jesus Christ.
The moment of truth had arrived! Even after several dry-run tests of the blower and its many connections, I still had the jitters! I had no real reason to feel this was because the entire project had been executed by skilled, professional technicians. Not yet knowing the ideal revolutions per minute (RPMs) needed to deliver the required four inches of wind, Mike set the motor to begin at 500 RPMs, 700 RPMs less than its top speed. #11887 was designed to deliver eight inches of static pressure, so we knew we wouldn’t need to run the motor at full capacity. Stan was ready to test the static pressure with a wind gauge meter.
I flipped on the main power switch at the console. The blower started. Stan’s meter indicated the static pressure to be too low, 2.7 inches of wind. We needed more RPMs, so Mike increased the speed to 900, still below its capacity of 1,200. The meter indicated 4.3 inches... BINGO! The moment had arrived to hear the organ at full throttle with an adequate wind supply! I pulled on every stop and played a HUGE chord. I was practically standing on the pedals! The sound was glorious... no sag in pitch whatsoever. Stan’s meter indicated that the static pressure, which naturally drops when the organ is demanding its maximum amount of wind, dropped only slightly to 4.1. This is a most ideal situation for any pipe organ. We truly had solved the problem. No more “short on wind†comments! Not only did we solve the wind problem, we solved a noise issue in the lower level of the church as well. This “new†old blower is twice the size of the 1985 model and is 95 years old, yet it runs trememdously smoother and quieter.
This project has been a labor of love. I am thrilled, pleased beyond words, and forever indebted to many businesses and individuals, listed below, for their input toward bringing a new energy in sound to our Johnson & Son pipe organ here at First United Methodist Church for the praise and worship of God and Jesus Christ.
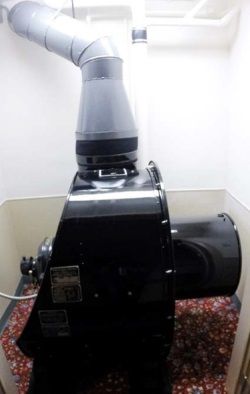
Installed #11887
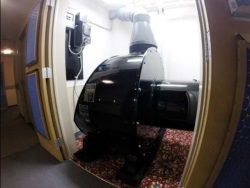
Assembled Orgoblo with new electric, wind line
and new filter brackets on the blower room doors
to help keep dust out of the organ.
and new filter brackets on the blower room doors
to help keep dust out of the organ.
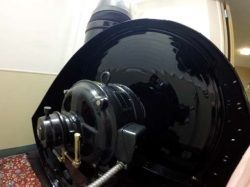
1921 Westinghouse motor, completely restored and
rewound - motor side of #11887
rewound - motor side of #11887
Thank You
Businesses/Associations
Businesses/Associations
Lakeside High School Music Boosters
Mr. William Hill
Mr. William Hill
J&J Excavating and Plumbing
Mr. Tim Barker and Mr. Brian Hampton
Mr. Tim Barker and Mr. Brian Hampton
Ohio Electric Motor Service Center
Mr. Mike Mosier and Staff
Mr. Mike Mosier and Staff
Dwyer Brothers Hardware
Mr. T.J. Dwyer and Mr. Traver Litchfield
Mr. T.J. Dwyer and Mr. Traver Litchfield
Buckeye Ford and Body Shop
Mr. Jim & Mrs. Jan Hunt, Mr. Jason Hunt,
Mrs. Kathy Beckwith and Staff
Mr. Jim & Mrs. Jan Hunt, Mr. Jason Hunt,
Mrs. Kathy Beckwith and Staff
McCombs Flooring
Mr. Bob & Mrs. Paula McCombs
Mr. Bob & Mrs. Paula McCombs
MCE Electric
Mr. Doug Peterman, Mr. Dustin Redding
Mr. Doug Peterman, Mr. Dustin Redding
Muller Pipe Organ Company
Mr. John Muller, Mrs. Jane Muller and Mr. Stan Osborn
Mr. John Muller, Mrs. Jane Muller and Mr. Stan Osborn
Nelson & Ball Heating and Cooling
Mr. Gene Ball and Mr. John Ball
Mr. Gene Ball and Mr. John Ball
Spencer Turbine Company
Windsor, Connecticut
Mr. Lester Raymond and Mrs. Linda Carter
Windsor, Connecticut
Mr. Lester Raymond and Mrs. Linda Carter
INDIVIDUALS
Mr. Paul Richards, Miss Lindsey Gibbs, Mr. Neil Pierce,
Mr. Kevin Lohr, Mr. Bryan, Mr. Owen and Mrs. Cindy
Shoemaker, Mr. Michael Schreffler
Mr. Paul Richards, Miss Lindsey Gibbs, Mr. Neil Pierce,
Mr. Kevin Lohr, Mr. Bryan, Mr. Owen and Mrs. Cindy
Shoemaker, Mr. Michael Schreffler
BOARD OF TRUSTEES
Mrs. Cindy Gross, Mr. Scott Higgins, Mr. Jamie Peart,
Mr. Bryan Shoemaker, Dr. Mitchell Spahn,
Mr. Tom Straley, Mr. Jim Weimer, Mr. Tim Wilson
Mrs. Cindy Gross, Mr. Scott Higgins, Mr. Jamie Peart,
Mr. Bryan Shoemaker, Dr. Mitchell Spahn,
Mr. Tom Straley, Mr. Jim Weimer, Mr. Tim Wilson